To make the most of your balcony when you can use it, especially if you don't live in a warmer climate where you can use it year-round. Long periods of disuse can cause damage to become invisible to the naked eye. A concrete balcony should be inspected frequently throughout the year to look for signs of wear and tear. Signs of trouble include rust spots, deck cracks, peeling coatings or paint, failing sealant, and loose or damaged railings.
Due to its strength, durability, and lifespan, concrete is often used for balcony construction. However, with time, the balcony's walls or floor become rough, cracked, or bumpy due to wear and tear, lack of care, incorrect installation, or exposure to the elements. Aside from being an eyesore, a growing crack in the concrete poses a serious safety risk. To make sure a crack doesn't get worse over the next six months, you should check on it regularly. If the fracture is shallow or hairline, you may fix it yourself; if it's deep or large, however, you should have a structural engineer examine the balcony to establish the reason of the crack and whether or not it can be fixed.
It is becoming increasingly common to use suspended access to fix concrete that has been eroded by water on balconies in high-rise buildings. Water that falls on the concrete balconies usually collects in puddles around the entrances, at least that's been my experience. The balcony's general condition is exacerbated by the amount of water that comes into contact with its outside border. When the damage to the concrete becomes too great for DIY restoration, a concrete repair contractor is called in to restore the concrete and offer concrete-based solutions for the project. The engineer's marks and the available square metres will define how much work needs to be done on the concrete. Clearly, this could shift depending on the gravity of the issues at hand. Work is done both to prepare the facility for sale and to address serious maintenance issues. Any issues that arise with concrete can be resolved by a professional concrete contractor. Check out Hitch Property Constructions for a wide range of balcony repairs.
Common Causes of Concrete Balcony Deterioration
Do you wonder what caused your balcony to crack and peel? Balcony deterioration is a regular issue for our contractors, and while there are a few common causes, it is conceivable that a professional examination will be necessary to pinpoint the particular problem. To put it simply, these are the most common reasons for issues that can usually be avoided:
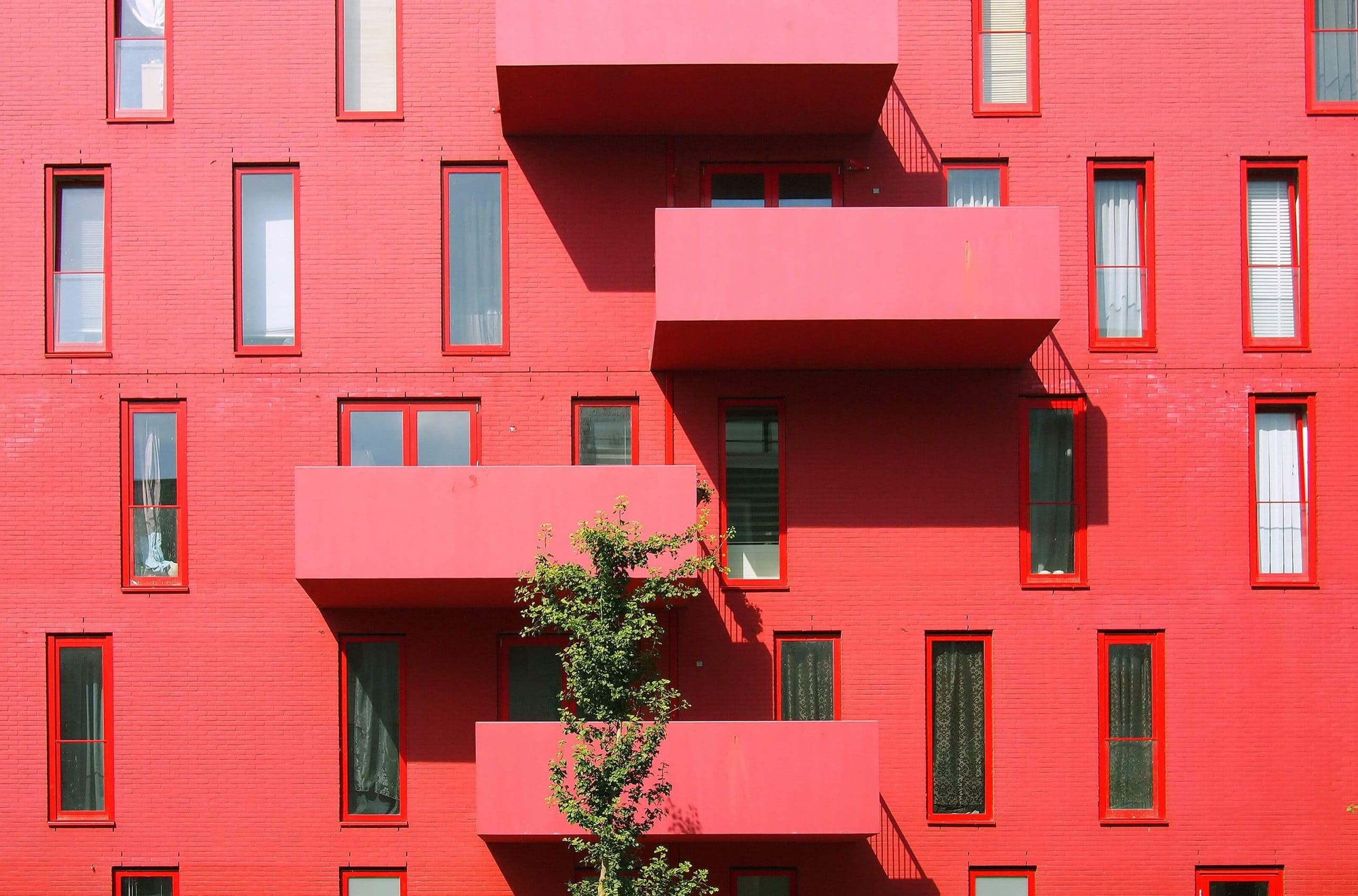
Waterproofing Â
If you don't properly treat or waterproof the slab tops and sides of your balcony, they may not last nearly as long. This is the kind of error that may really add up. When concrete is not protected by a waterproof coating, it is more vulnerable to the destructive effects of water and temperature fluctuations.
Adding deck tiles, rugs, or other floor coverings to your balcony can help you transform it into a stylish and comfortable outdoor room. These coverings can potentially damage the slab beneath them if the slab has not been properly waterproofed.
Sealing Â
Extra care must be taken to seal the joints where the balcony connects to the house or structure and where the railing posts are attached. Both the actual balcony and the spots where the railing posts are attached fall under this category. Without the proper sealer, the surrounding materials are left more vulnerable to wear and tear. You should "touch up" these spots every so often.
RustÂ
Damage and premature deterioration can be caused by rebar that is rusty, exposed, or located near the balcony's top surface.
Cracks Â
If you find gaps or cracks in the balcony slab, you should start sealing them right once. Unchecked growth could cause structural damage if the plants are permitted to expand too quickly. Even if the crack isn't huge, it's still crucial to treat the problem as quickly as possible.
Accessing the Balcony Concrete Repair
Maintenance of the swing stage's concrete. These high-rise concrete repairs are often accessed through suspended access equipment. These are known as swing stages, and their motors are made to operate on the building's strung suspension lines. The beams that make up our stage are currently resting on the top levels, and in this case we may need to employ jacks to provide additional support.
The Process for Concrete Repair on a High Rise Balcony
To repair a chipped balcony edge, concrete is first sawn off. Balcony concrete damage is being repaired by chipping away at it using chisels. All of the balcony railings need to be dismantled with a STIHL Metal Saw and a chipping hammer for the railing feet before access can be gained to the balconies. The concrete balcony repair that needs to be exhibited to the engineer is marked with marking spray, a chain, and a hammer. Fixing this issue is essential. Listening to the concrete requires the use of both the chain and the hammer. Sounds that are dull, hollow, or flaky are indicative of delaminations, and such locations will need to have the concrete removed.
In order to repair the concrete on the exterior of a high-rise residential building, a swing stage was installed. Our next step will be to remove the concrete from the drop where the stage will be once we have mapped out where each balcony will go. Having a hoist available to lift the rubble onto is a smart idea to explore in order to alleviate the strain that the debris would otherwise put on the stage. We'll also instal mesh around the stage to catch falling objects, and portable mesh on the ground level to catch debris from the demolition of the balcony's edge.
Close-up of the rebar that was cut out during repair work on a high-rise balcony. High-rise balcony concrete restoration; rebar is visible at the concrete's margins. We snapped our chalk line for the balcony's outer perimeter and then used a Stihl 420 Concrete saw to cut the concrete there. The massive blade allows for lightning-fast, pinpoint accuracy when cutting. If we simply cut through the concrete here, we can avoid having chipped and jagged edges in the final pour. Any extra concrete covering any exposed rebar must be chipped away with a hammer before the rebar can be inspected. Tying and doweling in new rebar when necessary. At the centre slab cuts, we remove concrete until we get a gap between the two layers of rebar that is about the width of two fingers. Then, the rebar is either coated or left unprotected after being wire wheeled with a grinder.
Preparing for the pour on the concrete repair
Plywood forms are pin-bolted into place with plywood bolts to fill the holes along the balcony's edge and any through slab voids that were produced. Drip edges for outer edge forms are made by attaching trim to the reverse side of the form. The water is able to drain away in this way. The Bosch Bulldog Max Hammer Drill will be used to drill pilot holes for the pin bolts that will fasten our forms to the existing concrete slab. Then, we'd use jacks to secure, modify, and finally establish a tight seal for our final form by placing them at each level. Removing the moulds when the pour was finished would have been much easier if we had used fewer pin bolts.
We used a hoist to help move materials around as we poured concrete. Individuals would be transported to the different levels with their finishing equipment and a pail of water and concrete to fill in any holes. The platform would also be equipped with a hose that would allow water to be poured onto the ground below. Once our hopper was fully loaded, the truck would take it to the correct level, where it would be lowered to the preexisting balcony. That's where they'd do the shovelling and load it into the moulds. Once the concrete has set and the work is done, we will return to remove the forms and cup polish the surface of the restored concrete to make it smooth and uniform.
Balcony Survey
First things first, get a professional architect or engineer to do a thorough survey. The engineer or architect will choose a row of apartments with balconies in visible disrepair and will use a scaffold to reach all of the balcony sections. The architect or engineer will "sound out" the concrete with a mallet to see if the balconies are still stable and to pinpoint the places that have been most damaged. Standing water is another warning sign that the balcony is not sloped correctly, causing water to pool instead of drain.
Unsafe and against code railings endanger the public.
The engineer or architect conducting the survey may request that the contractor perform investigative probes on the concrete in order to learn more about the subsurface conditions. Sometimes, a core sample of the concrete is taken at the request of the engineer or architect. To do this, you must first cut a 4-inch-wide circle into the concrete's surface, and then slice it all the way through. The concrete's compressive strength will be measured by subjecting a core sample to a battery of tests. The extent of damage over the entire concrete slab can also be determined with the help of these tests. The rusting of the steel reinforcement, which could undermine the structure, will be examined as part of the study. Keep in mind that the carpets, any coverings, and the aluminium cladding must be removed in order to get a clear look at the balcony surfaces and to conduct the probes.
Based on the survey results, the engineer or architect will advise on whether a full restoration is necessary or if a partial restoration will suffice. You should expect a balcony repair programme for your building to include replacing the rails and doing major concrete work. If the damage to the balconies is extensive, it may be necessary to demolish them and start over.
Looking for balcony repairs Melbourne? Look no further. Hitch Property Constructions has you covered.
Concrete Repairs
Although boards that are struggling financially might be tempted to engage a contractor to do temporary repairs like patching and caulking, this would just delay the inevitable and accelerate the degradation of the concrete. The damaged portions will need to have all of the concrete removed from them before they can be repaired properly. No bevelling or tapering of the cuts should be present. The next step is to scarify the sliced surfaces, which means to mechanically give them a rough texture. Bonding agent should be used towards the end to ensure proper adhesion of the fresh concrete to the old. Drip edges, which are shallow grooves that run the length of the underside of the balcony and begin a few inches in from the edge, should be installed if they do not already exist. This will help keep water far from the building.
Carpeting on balconies is a bad idea since it serves as a sponge, soaking up water and speeding up the concrete's degradation.
After any cracks or holes in the concrete are fixed, a non-slip traffic-bearing coating system should be applied to the balcony floor and kerb. The balcony fascia has a watertight coating. On the other hand, the underside of the surface is coated with a permeable material to allow for vapour transmission and ventilation. Coating systems can be found in an abundance of colours.
Ironically, the amount of ponding that happens might be made worse by restoring the concrete balconies and coating systems. When two things interact in an unexpected way, we get a paradox. First, the non-permeable coating method ensures that water does not penetrate the repaired cracks in the concrete, so any water that was previously seeping into the concrete remains on the top. In order to achieve this goal, it is important to repair concrete surfaces so that water cannot penetrate them. Second, if the balcony is not sloped away from the door leading to the balcony, water will pool in low spots. A fresh layer of sloping concrete will need to be poured to the area to correct the issue by creating a gradient allowing water to flow down and away from the region.
Aluminum Cladding
Some people will put cladding over their balcony kerbs, either as an extra layer of defence after they've been built or as a misguided attempt to prevent water seepage through damaged concrete. Cladding made of aluminium can be used to keep concrete from falling apart in emergency scenarios. Water will eventually find a way through aluminium, at best. Over time, the cladding tends to loosen, allowing more water to seep in and collect. As a result, the concrete below will be severely damaged. The margins of the balcony should be visible when repairs are performed.
Railings
Loose, rusty railings should be fixed or replaced as needed. First, the concrete railing posts must be removed from the concrete, and then the damaged concrete must be removed. Epoxy should be used to fill the gaps in stainless steel sleeves into which the posts are placed. Another option is to just slide the posts into the epoxy. An occasional necessity is the installation of a cushioned filler called a backer rod, which is sealed off with caulking at the base of the post penetration into the concrete, to prevent water from entering.
Aluminum could be a good alternative to metal if you need to replace the entire railing system. Aluminum, once correctly finished, does not rust and hence requires far less upkeep than metal does, as it does not need to be scraped, primed, or painted on a regular basis. The distance between the top of the railing and the balcony surface may be reduced if a layer of concrete is added to the balcony to obtain the suitable slope for drainage (as indicated above). The engineer or architect tasked with designing and specifying the railing must account for the height differential when determining the extent of the necessary repairs. No major upkeep of the additional balconies is expected to be necessary.
Given that the building will soon be undertaking a facade restoration programme, it makes sense to incorporate the balcony work into the overall repair timetable in order to avoid paying twice as much for mobilisation and scaffold costs. Since the contractor would probably work on one apartment line at a time, the board should have plenty of time to notify tenants that they must remove all items from their balconies (including furniture, planters, carpets, and personal items). Typically, the contractor will focus on a single apartment building at a time.
Maintenance
The new balconies should require minimal maintenance after the repairs have been made. The caulking around the railing posts should be inspected regularly and recaulked if necessary to prevent water from penetrating the posts and causing damage. Residents should be mindful not to harm the coating system on their balconies by dragging furniture or other objects with sharp edges across the surface. Residents should be cautious when clearing the debris off the balcony.
Finally, residents should avoid carpeting their balconies since it functions as a sponge for water, keeping the balcony's surface moist and hastening its degradation. Carpeting not only makes it harder to maintain, but it can also cover up cracks.
You can't get away from the following: Although a thorough balcony repair programme is a major effort, it should not be put off. It needs to be treated with the same care as other major outdoor projects to ensure the safety and satisfaction of the locals.
Repairing Concrete Floor
Step 1
When cleaning the concrete on your balcony, use a pressure washer fitted with a fan tip. To clean the concrete floor, hold the washer 8 inches above it and move it in slow sweeps to loosen and remove the built-up dirt and debris. The floor's flaws will become readily apparent.
Step 2
Any floor damage can be patched up with concrete repair caulk. Drag your finger across the caulk's surface until it's as smooth as you can get it. Be sure to let the caulk dry for the full period of time specified on the packaging before applying it.
Step 3
Using a 5-gallon bucket, mix the concrete dressing as directed by the manufacturer.
Step 4
Dressing in hand, spread it out over the balcony's floor and immediately press it into the gaps and cracks with a trowel. You should have an assistant rapidly mix up another batch of concrete and pour it around the remaining pieces of the floor to finish the massive balcony.
Step 5
Wet concrete can be made safer by sweeping it with a broom that has medium-sized bristles. It's important to let the concrete cure for the time period recommended by the manufacturer.
Repairing Concrete Walls
Step 1
Rub the fissure in the concrete wall with a hard wire brush to remove any loose debris. You can use a shop vacuum to clear up the mess that the debris has made. Verify if the crack is dry, and if it isn't, use a blow dryer to impart intense heat to the crack for twenty minutes.
Step 2
Hammer three-inch finishing nails at 12-inch intervals along the crack's length. Nails should be hammered in until they are halfway through the concrete.
Step 3
Crack sealer comes in two parts; mix them together as directed on the label, using a piece of scrap wood. Distribute it uniformly on the bottom of the plastic repair port the package provides. First, slide the port's base against the wall, then move it up until it completely covers the nail. To finish installing the ports along the fissure, you will need to start over.
Step 4
After spreading repair epoxy into and over the fracture, the crack should be expanded by one inch on each side. Use a putty knife to spread the epoxy around the port's base and flange. Try not to block the ports' openings with anything. Don't use the epoxy until it has cured for the full amount of time specified on the bottle.
Step 5
To use the liquid epoxy that included with the repair package, load the caulk tube into the caulking gun. Just keep injecting it into each port until epoxy starts flowing out. Cover the openings with plastic caps. The filler needs to cure for five days.
Hitch Property Constructions has a wide range of the Melbourne balcony repairs right here.
Step 6
Remove the plastic ports' protruding necks using the hacksaw, and then set them flat with the concrete wall.
When fixing a balcony, the first step is to determine how much concrete upkeep is needed. Exposed to the elements in the north-east, even minor fractures in the concrete of a balcony, such hairline cracks, will become a major hazard. The first order of business is to determine what's caused the decline so that the root causes may be addressed. After the root reasons have been isolated, qualified professionals will fix the concrete balcony and replace any damaged railings.
All deteriorated concrete and steel must be removed, corroded reinforcing steel must be exposed, the remaining exposed steel and concrete must be surface prepared, and a patching material with properties similar to the original concrete must be applied in order to repair or replace a balcony made of concrete. Restoring your balcony will last for years to come if the proper treatment is applied to the steel and concrete.
Conclusion
When something sits unused for a long time, the wear and tear can become imperceptible. It's important to keep an eye out for cracks and other damage to a concrete balcony all through the year. Problems can be identified by the presence of corrosion, fractures in the deck, peeling paint or coatings, deteriorating sealant, and unsecured or broken railings. Contractors frequently report problems with deteriorating balconies. An expert evaluation is needed to identify the precise issue.
Dress up your balcony floor with deck tiles, rugs, or other floor coverings. If the slab beneath these coverings has not been properly waterproofed, it may be damaged. Concrete must be sawed off the damaged edge of a balcony before it can be repaired. The chain and the hammer are both necessary for listening to the concrete. Dull, hollow, or flaky noises are signs of delaminations.
The concrete needs to be removed from these spots. In order to guarantee the safety of the balconies in question, an architect or engineer will conduct a complete inspection of the area. They would come back once the concrete had hardened to remove the moulds and polish the finished product. The contractor may be asked to run exploratory probes into the concrete by the surveying engineer or architect. The results of these analyses can also be used to assess the level of damage across a whole concrete floor.
It may be essential to dismantle the balconies and start over if the damage is severe. It is possible to stop water from leaking into the concrete below by repairing the balconies and painting them with a non-slip traffic-bearing coating. While aluminium cladding can be utilised to prevent concrete from crumbling in an emergency, it will not stay waterproof forever. If you need to replace the complete railing system, aluminium could be an excellent choice to metal. The new balconies should not require any significant repairs.
In some cases, a layer of concrete can be used to shorten the height between the top of the railing and the balcony floor. Make use of a pressure washer with a fan tip to clean the concrete on your balcony. You must wait the manufacturer-recommended amount of time for the concrete to cure. After applying repair epoxy, it should be enlarged by an inch on either side of the fracture. The first step in repairing a balcony is establishing the level of concrete maintenance required.
Balconies in the north-east are particularly vulnerable to the weather, and even small cracks in the concrete can quickly become severe hazards. If the steel and concrete on your balcony are treated properly, the restoration work you do now will survive for many years.
Content Summary
- A concrete balcony should be inspected frequently throughout the year to look for signs of wear and tear.
- Aside from being an eyesore, a growing crack in the concrete poses a serious safety risk.
- Any issues that arise with concrete can be resolved by a professional concrete contractor.
- Do you wonder what caused your balcony to crack and peel?
- To repair a chipped balcony edge, concrete is first sawn off.
- In order to repair the concrete on the exterior of a high-rise residential building, a swing stage was installed.
- Close-up of the rebar that was cut out during repair work on a high-rise balcony.
- Plywood forms are pin-bolted into place with plywood bolts to fill the holes along the balcony's edge and any through slab voids that were produced.
- Once the concrete has set and the work is done, we will return to remove the forms and cup polish the surface of the restored concrete to make it smooth and uniform.
- Sometimes, a core sample of the concrete is taken at the request of the engineer or architect.
- You should expect a balcony repair programme for your building to include replacing the rails and doing major concrete work.
- After any cracks or holes in the concrete are fixed, a non-slip traffic-bearing coating system should be applied to the balcony floor and kerb.
- Aluminum could be a good alternative to metal if you need to replace the entire railing system.
- No major upkeep of the additional balconies is expected to be necessary.
- The new balconies should require minimal maintenance after the repairs have been made.
- When cleaning the concrete on your balcony, use a pressure washer fitted with a fan tip.
- To use the liquid epoxy that included with the repair package, load the caulk tube into the caulking gun.
- Cover the openings with plastic caps.
- Remove the plastic ports' protruding necks using the hacksaw, and then set them flat with the concrete wall.
- Restoring your balcony will last for years to come if the proper treatment is applied to the steel and concrete.
FAQs About Balcony Repair
You are able to pour new concrete on top of the existing concrete. If you do not take the necessary precautions, however, problems with your old concrete that have not been resolved, such as cracks or frost heaves, will be transferred to the new concrete. Additionally, you are required to pour it so that it is at least 2 inches thick.
A crack isolation membrane, such as Ditra or NobleSeal, might be effective in repairing horizontal cracks in the concrete. If the cracks exhibit vertical shear, which means that one side is higher than the other, there is nothing that can be placed over the slab to protect the tile from further cracking, and doing so would be a waste of your time and money.
You can easily and quickly apply flooring-specific liquid membrane waterproofing to the finished floor using rollers or brushes for balcony floors that do not have cracks or tenting. This type of waterproofing is designed specifically for flooring. If the process is carried out in accordance with the directions provided by the manufacturer, there should be no gaps left behind, and the resulting thickness should be no more than a few millimetres.
Using a paint brush, coat the aged concrete that is still damp with a very thin layer of the cement paint. Carry out this step immediately before you intend to pour the new patch of concrete onto the existing concrete surface. Just before applying the concrete patch, whether it was homemade or pre-mixed, add the water to it. Combine it carefully.
Sealers that form a film on the surface of the concrete and sealers that penetrate the surface are the two primary categories of concrete sealers. Sealers that form a film on the surface of the concrete include acrylics, epoxies, and urethanes. This coating protects the concrete from moisture. Film-forming sealers, particularly acrylics, are more prone to wear and need to be reapplied more frequently than other types of sealers.