Balcony leaks are prevalent, especially in older homes, and if left unresolved, they can cause serious structural damage. Termites prefer moist environments, so make sure to avoid leaving any water sitting about. The last thing you need is a termite infestation if you've already got mould growing around your house. If your balcony is leaking, you need to get it fixed right away so that it doesn't cause any other problems. It is not necessary to tear out tiles and replace the waterproof membrane to make a balcony watertight; instead, you can use a balcony sealant to achieve the same result in as little as one day for a fraction of the cost, not to mention the savings in the long run from not having to deal with termites.
Check out Hitch Property Constructions for a wide range of balcony repairs.
How to Waterproof Decks and Balconies
Before anything else, the deck's orientation must be taken into account. Depending on the final use of the deck, the deck may be buried or left exposed, making it susceptible to environmental wear and tear. As a result, it is crucial that the right products be specified. Because balconies are often situated in the air, the available product selections tend to be less difficult.
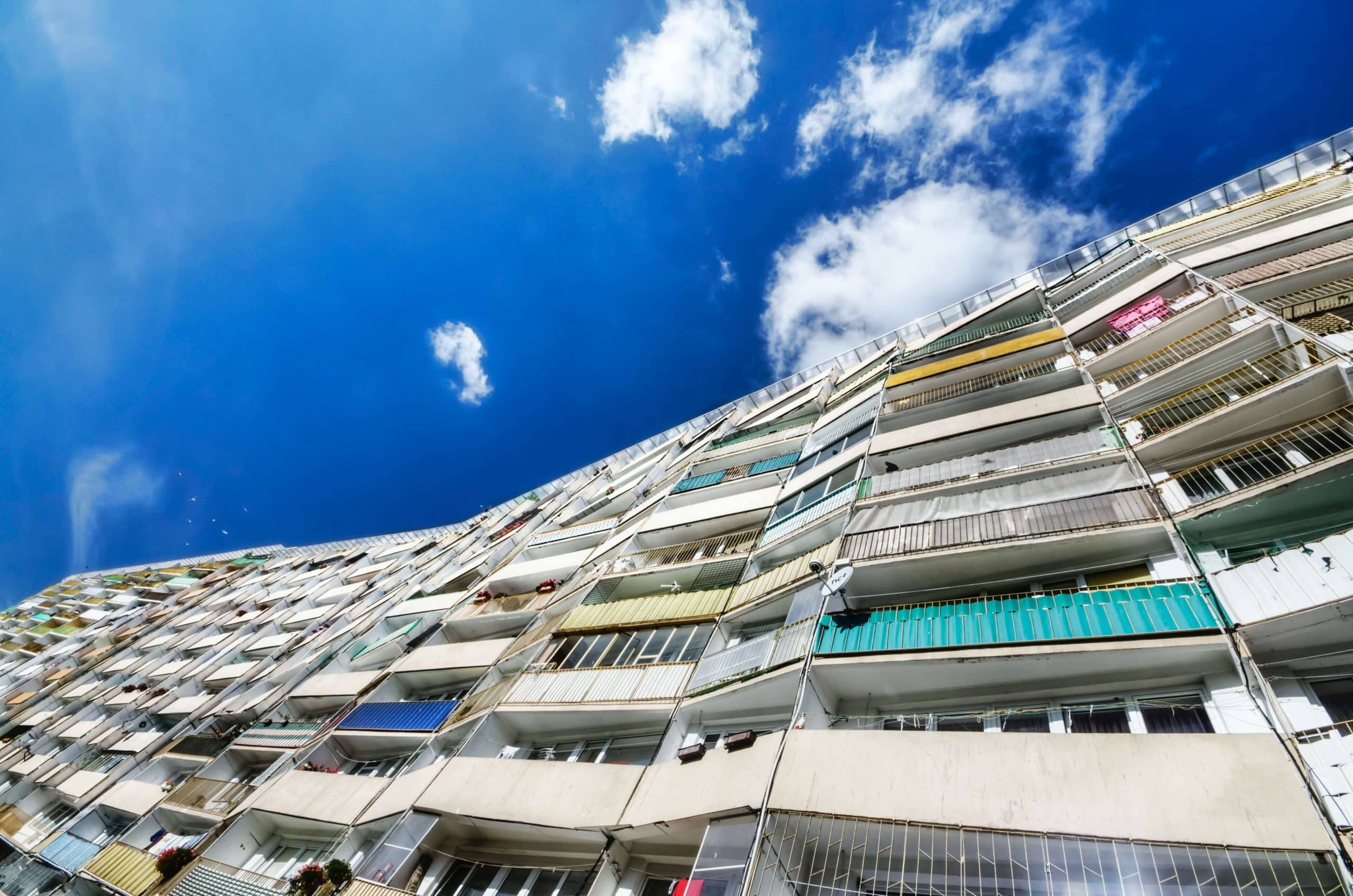
How to Decide Which Products to Use
When the deck is open to the elements and vulnerable to wear and weathering, it is especially important that the waterproofing product has a strong adhesion to the substrate it is applied to. Materials used to waterproof the deck in this instance should also be resistant to the effects of ultraviolet light and slippery in wet conditions.
Waterproofing concrete decks is an important service that Newton offers in a variety of forms. All bases are covered with primers, wearing coats, multi-coat systems, drainage membranes, and vapour-permeable and vapour-impermeable membranes. Considering both the project's intended function and its geographical context is crucial when deciding which product(s) to use. If your deck is exposed to the elements, you'll want to choose different materials than you would if it were covered.
If you need help creating a solution that is unique to your project, the technical professionals at Newton can give you a hand.
What to consider before waterproofing
The designer of a brand new house must decide on the best strategy for waterproofing the outdoor flooring. Common practise today calls for a drainage membrane to be applied to the underside of a substrate to help ensure proper waterproofing. According to UNI11493-1, "the indication of a drainage and protection membrane, applied between the substrate and water barrier is a measure with the purpose of avoiding water stagnation from reaching the structure." The purpose of this precaution is to stop water from being trapped inside the building.
However, when it comes to making improvements, it's important to weigh several different variables to determine which option best meets a set of basic needs.
In this case, it is crucial to first examine the area that will host the intervention:
- Find out how badly the flooring and substrate have been damaged.
- Verify the accuracy of the layered structure.
- It's crucial that the flooring has an acceptable slope.
- Examine the various levels to make sure there are no splits or holes in them.
Based on the details presented below, pick the option that works best for the specific balcony or patio in question.
Choose the most suitable waterproofing solution for renovations.
You may choose the best option for the outside space by analysing several criteria and making a call based on the results. If the flooring is in immaculate condition, you may be able to skip the subfloor entirely and just waterproof the flooring itself.
However, if the tiles have damage like cracks or holes, it's best to get rid of them and then waterproof the substrate layer underneath. If the substrate itself is in poor shape, waterproofing the layer below it is your best bet for stopping any leaks in the future. If making the layer watertight is the most effective option, this will be the result.
Waterproofing solutions without removing the tile
If the flooring is in good shape and there are no cracks or tenting, liquid waterproofing is a great solution that can be used instead of having to remove the tiled surface. It can be rolled or brushed across the entire surface in a short amount of time without leaving any gaps, and it only results in a thickness that is a few millimetres high. Liquid membranes can be used in this way to create a system that is impervious to the effects of heat, cold, chemicals, or even standing water, provided that the process is carried out in accordance with the manufacturer's instructions. Procedures for this should be carried out in strict accordance with guidelines provided by liquid membrane suppliers. One crucial consideration is whether or not the new flooring will be compatible with the existing one; this is something to address with the service provider.
Waterproofing solutions between tile and substrate
In the event that the floor is broken or unusable, it must be taken up so that repairs can be made to the layer directly beneath it, which sits atop the substrate. Having this ready is necessary in the event that the flooring needs to be replaced. Waterproof membrane rolls and waterproofing solutions are two of the most often used waterproofing methods.
Rolled membrane waterproofing systems
Waterproofing the substrate with rolled membranes is a common problem, and there are many products on the market to address this issue. Most commonly used are bituminous, rolled, self-adhesive waterproofing membranes that may be put on-site using hot air welding.
The substrate must be absolutely dry, dust-free, and immaculate. Applying thinset mortar is the next step before tiling after adhesive membranes have been installed.
If the waterproof layer beneath the substrate has not been damaged, a more hygienic and quicker alternative, such as a rolled-up polythene membrane, can be used. Our go-to recommendation for this sort of waterproofing is Floortec, a membrane made from polythene with a non-woven cloth fused to its underside. With a total thickness of only 3 mm, Floortec not only increases load resistance but also reduces structural stress, controls rising moisture during installation, and fortifies the waterproofness of the substrate. Floortec's 3-millimeter total thickness allows it to give all of these advantages while yet being incredibly practical. The tiles can be installed after an adhesive cement has been used to secure the membrane to the cement subfloor.
Cement-based liquid compound waterproofing system
As an alternative to a bituminous membrane, you may apply an easily spreadable liquid cement layer on top of the substrate. The final product is a cement-based mixture to which water-resistant polymers and other ingredients have been added. The next steps are to apply a tile glue and then the tiles. It's easier than the previous method. On the other hand, in real life, the cement layer is not entirely watertight. In the event of temperature changes, the cement layer may expand or contract, allowing a trace amount of moisture to permeate the layer below. Restoration projects where it is known without a shadow of a doubt that the substrate is in pristine condition, free of fractures or even minute fissures, are prime candidates for this approach.
Looking for balcony repairs Melbourne? Look no further. Hitch Property Constructions has you covered.
Waterproofing solutions under the substrate
The only option to stop further degradation from happening and fix the infiltration problem is to intervene beneath the substrate. In order to comply with regulation UNI11493-1, a waterproofing layer should be laid, followed by a drainage membrane that acts as a barrier and allows water to drain freely from the draining substrate above. The waterproofing layer should be on first, followed by the drainage membrane for the greatest effects.
Bituminous membrane waterproofing system
Commonly used for waterproofing the space under the substrate of terraces and balconies, bituminous membranes are a quick and easy solution. These membranes are made from crude oil distillation and are commercially available in premade rolls. The roll's thickness also conceals a resistance-increasing armature. Fiberglass or polyester can be used to construct the armature.
For pedestrian areas, a bituminous membrane with a thickness of 4 millimetres is suggested. This is done to boost the material's mechanical resistance and keep its unique elongation property. Outdoor spaces like balconies and patios are prime examples of pedestrian zones. Flame bonding on the sheets of prefabricated rolls makes installation easy and guarantees a secure hold on the surface.
These same membranes can also be purchased with an adhesive layer, making them suitable for use in situations where an open flame would be unsafe. Though these are easier to use, they sacrifice some of their potency in the process.
The importance of draining membranes
Drainage membranes that are laid out beneath the building's substrate save the day for the building's overall stability.
Most damage to balconies and terraces is caused by water, which eventually seeps into the interior of the substrate and erodes the many waterproofing layers over time. The drainage membrane has a unique design that ensures this kind of problem never arises. Because of the hydrostatic strain that develops between the substrate and the bitumen-based membrane, our experts advise using Draintec 8, a membrane that was developed by our team specifically to facilitate water drainage via a network of drainage channels.
This item's unusual shape serves two purposes: it supports the load and reduces the load compression that occurs when people or things pass through it. Even though it's only 8 mm thick, Draintec 8 consists of two bonded layers. The first is a cone-shaped element polythene base for separating and draining liquids. In order to create the membrane's second layer, a non-woven fabric is layered on top of the substrate. With this layer in place, the membrane's channels are protected from dust and other tiny debris that could clog them and reduce the membrane's overall effectiveness.
Draintec 8S is a netting with a more open weaving structure than Draintec 8 and is the superior choice when a substrate that drains water is required.
Using a perimeter profile for optimal results
If you're hoping for cutting-edge results from your involvement, we advise installing the Border Tex BD profile along the entire periphery of the patio or balcony. The drainage holes in this edge profile serve the function of quickly and efficiently dispersing any standing water. The Bordertec BD should go between the drainage membrane and the bituminous membrane, which is located beneath the substrate. When combined with a drainage membrane like Draintec 8, this product provides unmatched protection against infiltration and structural damage for a terrace.
Balcony Waterproofing
It's not uncommon for residential buildings to have issues with the waterproofing of their bathrooms and balconies, and fixing either may be quite expensive. The issue of water resistance on a balcony is particularly difficult to solve. Because tearing up the floor people walk on to make repairs is not a simple task, you only get one chance to get it right when using tiles.
Installing Butyl Rubber
Waterproofing a balcony is similar to other types of construction in that it requires a solid foundation. While the specifics of this substrate may vary from system to system, a reasonable rule of thumb is to give a finish that you would be comfortable tiling over without the use of any additional waterproofing substance.
The Waterproofers advise that no silicone or polyurethane be used on a balcony before they arrive to apply the waterproof coating. Leak control flanges, or floor wastes, have silicone applied to them and their edges sealed rather often. This silicone might potentially disrupt certain of our systems, making it impossible for us to do our tasks. We expect the contractors to make every effort to ensure a watertight seal before they leave the job site. However, these methods occasionally prevent us from offering a solution that will satisfy the client.
All of the standard product lines we employ can be used to effectively waterproof balcony areas. There are a variety of systems to choose from, each with their own set of benefits and considerations that must be made when determining which is the best option for your project. If you need help deciding how to proceed with this matter, feel free to get in touch with us. Torch-on bitumen membranes are highly flammable and should not be used on an outside space like a balcony. Despite being a trafficable membrane system, they struggle to deal with the strain of heavy foot traffic on hot days. Bitumen that has been left to soften is more easily damaged and transferred to your shoes, where it can be tracked inside your home.
Butyl Rubber Waterproofing
Butyl rubber is a great membrane to use when waterproofing balconies since it can be laid either beneath a screed or immediately below most surface treatments. Almost any surface can have a layer of butyl rubber applied to it to make it waterproof, so long as it meets a few basic requirements. Concrete, plywood, and cement sheet are all examples of substrates. Before a butyl rubber waterproofing membrane is laid down, an epoxy primer is sometimes used first.
Waterproofing the screed with a second membrane after the butyl rubber coating has dried is necessary to prevent efflorescence from pushing up through the screed and ruining the finished surface. This is essential when laying a waterproof screed above butyl rubber. This membrane could be yet another layer of butyl rubber, or any of the numerous varieties of seamless liquid membranes available.
Before installing the door and window frames, as well as any other wall treatments, butyl rubber must be coated and glued to the building framework (or masonry). Considering the use of a butyl rubber, this is another factor to consider. As the "leaky building syndrome" in New Zealand's housing market shows, this is especially important as lightweight foam is increasingly used in construction.
Tiles and other finishing materials are the final major consideration once butyl rubber has been used to waterproof a balcony. Butyl rubbers are notoriously difficult to attach to due to their unique qualities; as a result, most tile adhesives have a hard time forming strong enough connections to hold the tiles in place. It would be to your advantage to bring up the matter of the finishing material when we discuss your project.
Hitch Property Constructions has a wide range of the Melbourne balcony repairs right here.
Seamless Liquid Waterproofing
Waterproofing a balcony with a liquid system is not as as forgiving as waterproofing a balcony with a butyl rubber system, but it can be done later in the construction phase, reducing the risk of damage. It is important to prime the substrate to ensure a good adhesion of the final product; epoxy primers may be required in some cases if the substrate is particularly difficult to prime.
It is not necessary to initially attach the door frames and wall cladding when using a liquid to waterproof a balcony, as is the case when using butyl rubber. Where the membrane does not cover the full wall, the flashings should be fixed loosely behind the cladding and should extend far down onto the balcony floor.
When it comes to the finishing touches, liquid waterproofing systems are more flexible and can work with more adhesives. Similar to the previous point, these need to be discussed before work begins to ensure that compatible goods are used.
Some balcony waterproofing options include the use of liquid membrane systems. These systems provide a waterproof barrier as well as a durable coating that is suitable for high-traffic areas. In situations where cost-cutting is a priority or where saving weight is of paramount importance, these methods really shine.
You may already be aware of the significance of waterproofing your outdoor deck to the security of your property. Waterproofing a deck prevents mildew and dry rot from establishing themselves there. You probably don't give the procedure of waterproofing a balcony much thought. If you want to know if waterproofing your balcony is necessary and why it is, read on!
If you're concerned about protecting the people who matter to you most in the world, you can either do it yourself as a do-it-yourself project or hire a professional contractor. The balcony must be waterproofed. This is especially true if your balcony's frame is made of wood, as these balconies have a far higher failure risk than other types. Wooden-framed balconies are susceptible to a wide variety of problems, including leaks, obvious damage, and even hidden harm. These hidden damages, which might include structural deterioration, can be brought on by dry rot. Dry rot, which spreads from the inside out, weakens the structural integrity of wood. A good approach to check for dry rot in wood is to press down on it with your palm or foot. If the wood has a spongy texture and doesn't feel like a regular hard surface when pressed, dry rot is likely to be present.
No matter how sturdy your concrete balcony may be, you still need to keep up with routine maintenance. In addition, concrete buildings need to be waterproofed. Waterproofing the concrete serves to fortify it against future deterioration caused by contact with liquid water. Waterproofing concrete also prevents the growth of mould and mildew and shields against UV radiation. Important since most balconies get a lot of direct sunlight that contains harmful UV rays. Waterproofing your balcony will save you money in the long term, which is something to think about. Water damage repairs to a deck almost always end up costing more than the expense of waterproofing the deck in the first place. Waterproofing should be a top priority if your balcony is located in a high-risk area.
Conclusion
Newton provides a number of options for effectively waterproofing concrete decks. When picking on a product or products to employ for a project, it is important to keep in mind the project's function as well as its location. Using a different set of materials on an uncovered deck might be wise than on an exposed one. A new home's architect is responsible for determining the most effective method of waterproofing the exterior flooring. As standard procedure, drainage membranes are typically installed on the underside of a substrate.
The waterproofing layer beneath the substrate is the best bet if the substrate is in bad shape. Instead of tearing up the tiled surface and starting over, you may use a liquid waterproofing solution, which is a far more convenient and cost-effective option. Rolls of self-adhesive bituminous waterproofing membranes are the industry standard. After the adhesive membranes have been put, thinset mortar must be applied before the tiling can begin. The subflooring of balconies and terraces must be waterproofed to prevent water damage.
Substrate drainage membranes save the day for structural integrity. Prefabricated roll sheets are flame bonded for a strong surface grip and simple installation. Water seepage into the interior of the substrate is the primary source of damage to balconies and terraces. We choose Draintec 8 for balcony waterproofing due to the hydrostatic strain that arises between the substrate and the bitumen-based membrane. Before the Waterproofers arrive to apply the waterproof coating, they ask that no silicone or polyurethane be used on the balcony.
Choosing the most appropriate system for your project might be challenging because there are many viable options. In order to prepare the building for the installation of the door and window frames, butyl rubber must be coated and attached to the framework (or masonry). Preventing efflorescence from breaking through the completed surface requires waterproofing the screed with a second layer. Liquid waterproofing methods have greater adaptability and compatibility with a wider variety of adhesives. To prevent water from seeping through, some balcony owners choose to instal a liquid membrane system.
Deck mildew and dry rot can be avoided with proper waterproofing. It is more expensive to repair water damage to a deck than to waterproof it.
Content Summary
- The designer of a brand new house must decide on the best strategy for waterproofing the outdoor flooring.
- Common practise today calls for a drainage membrane to be applied to the underside of a substrate to help ensure proper waterproofing.
- Choose the most suitable waterproofing solution for renovations.
- If the flooring is in good shape and there are no cracks or tenting, liquid waterproofing is a great solution that can be used instead of having to remove the tiled surface.
- Having this ready is necessary in the event that the flooring needs to be replaced.
- As an alternative to a bituminous membrane, you may apply an easily spreadable liquid cement layer on top of the substrate.
- Because of the hydrostatic strain that develops between the substrate and the bitumen-based membrane, our experts advise using Draintec 8, a membrane that was developed by our team specifically to facilitate water drainage via a network of drainage channels.
- Using a perimeter profile for optimal resultsIf you're hoping for cutting-edge results from your involvement, we advise installing the Border Tex BD profile along the entire periphery of the patio or balcony.
- The Bordertec BD should go between the drainage membrane and the bituminous membrane, which is located beneath the substrate.
- When combined with a drainage membrane like Draintec 8, this product provides unmatched protection against infiltration and structural damage for a terrace.
- Before a butyl rubber waterproofing membrane is laid down, an epoxy primer is sometimes used first.
- This is essential when laying a waterproof screed above butyl rubber.
- Before installing the door and window frames, as well as any other wall treatments, butyl rubber must be coated and glued to the building framework (or masonry).
- Tiles and other finishing materials are the final major consideration once butyl rubber has been used to waterproof a balcony.
- It is not necessary to initially attach the door frames and wall cladding when using a liquid to waterproof a balcony, as is the case when using butyl rubber.
- When it comes to the finishing touches, liquid waterproofing systems are more flexible and can work with more adhesives.
- Some balcony waterproofing options include the use of liquid membrane systems.
- The balcony must be waterproofed.
FAQs About Balcony Repair
Bituminous membrane waterproofing system
When it comes to waterproofing the area beneath the substrate of terraces and balconies, the most common method is to use bituminous membranes.
A completely waterproof seal is produced above and below your deck when a Tufdek vinyl membrane is installed on a second-story deck, regardless of whether the deck is new or already in place. If you have a vinyl deck, the water will run off the edge of the deck rather than getting trapped in the cracks. Both the space underneath your deck as well as the space above it are totally safe.
When applying Shower Plug or Resistain sealant, you can do so with a brush, roller, or spray. Sealant should be liberally applied to the surface after dipping the brush or roller in the bucket of sealant and then applying it. – Fill up the entire surface with the liquid. In order for it to be fully effective, it must absorb the maximum amount of liquid sealant that it can over the course of two coats.
Your balcony can be resealed with epoxy regrouting, which eliminates the need to remove the tiles. a substance that can withstand the effects of both water and chemicals. It requires little to no maintenance and can withstand any kind of weather. As an additional safety precaution, we will also apply polyurethane silicone to all of the junctions along the perimeter.
Tiles made of porcelain are readily available and have quickly become one of the most popular choices for the flooring material on balconies. The fact that these tiles are extremely dense and long-lasting makes them an excellent choice for use in outdoor settings.